Jugend-Forscht Beitrag 2000 (von A. Härtel)
Der Computer destilliert
©by Andreas Härtel (von Andreas Härtel)
Düsseldorf, den 16. Januar 2000
Inhalt:
- Kurzfassung
- Ziel und Sinn der Arbeit
- Die Idee
- Die erste Umsetzung
- Die zweite Umsetzung
- Die aktuelle Umsetzung
- Die Apparatur
- Die Temperatursensoren
- Die Hardware
- Die Software
- Lehrmöglichkeiten
- Das Handbuch (siehe auch: Handbuch)
- Ein Anwendungsbeispiel
- Die aufgetretenen Probleme
- Verbesserungsvorschläge für zukünftige Arbeiten am Projekt
- Quellenangaben
Kurzfassung:
In meiner Arbeit habe ich ein selbst entworfenes Interface entwickelt und aufgebaut, welches in erster Linie als Bausatz für Schulen dienen soll.
Es ermöglicht die Steuerung eines 220V~ Anschlusses und die Messung der Temperatur mit Hilfe eines temperaturabhängigen Widerstandes über die parallele Schnittstelle des Computers.
In diesem Fall steuert der Computer ein elektrisches Heizkissen und kann somit eine eingegebene Temperatur beibehalten. Dies wird für einen vom Rechner gesteuerten Destilliervorgang ausgenutzt.
Mit diesem Bausatz soll es Schülern ermöglicht werden, physikalische, chemische und informatische bzw. mathematische Zusammenhänge anhand von praktischen Beispielen zu erlernen. Außerdem wird durch die große Anzahl von am Thema beteiligten Fächern ein fächerübergreifendes Lernen ermöglicht.
Der Bausatz kann zum Beispiel im Physikunterricht aufgebaut werden; dabei kann den Schülern unter anderem das Ohmsche Gesetz sowie die Wirkung von zusammen geschalteten Widerständen oder die Arbeitsweise elektrischer Bauteile vermittelt werden. In den Aufbau lassen sich auch Informatikkurse mit einbeziehen. Es können Bits und Bytes und deren Wirkung im Rechner oder einfach die parallele Schnittstelle untersucht werden. Auch das Erarbeiten eines eigenen Steuerprogramms wäre denkbar.
Aber auch im Chemieunterricht kann anhand des Bausatzes Wissen vermittelt werden. Es können zum Beispiel beim Ätzen der Platine des Interfaces die Reaktionen von Säuren mit Metallen erklärt oder mit der fertigen Arbeit die Siedepunkte verschiedener Stoffe untersucht werden.
Die bisher genannten Punkte würden für sich genommen eher zum Themenbereich "Arbeitswelt" gehören! Da es jedoch beim Planen und Bauen des Interfaces mehr um die Automatisierung des Destilliervorganges ging, habe ich den Themenbereich "Technik" gewählt.
Entsprechend gestaltete sich auch die zu erledigende Arbeit:
Es mussten Messungen durchgeführt, Programme geschrieben und Schaltungen auf- und abgebaut werden.
Im Endeffekt besteht die Arbeit aus einem technischen Mittel zur Verbesserung der Arbeitswelt.
Anmerkung: Meine Arbeit könnte auch als Bausatz für den privaten häuslichen Gebrauch verkauft werden.
Ziel und Sinn der Arbeit:
Das Ziel dieser Arbeit besteht in der Automatisierung des Vorganges einer Destillation. Dies ist zwar in der Industrie gewiss schon geschehen, aber nur in industriellen Maßen. Die vorhandenen Anlagen dürften somit die finanziellen Möglichkeiten sowie den zur Verfügung stehenden Raum eines Privatmannes oder einer Schule bei weitem übersteigen.
Aus diesem Grund habe ich eine kleine, viel preiswertere, Apparatur entworfen und aufgebaut, die lediglich einen Computer mit einer parallelen Schnittstelle und dem Betriebssystem Windows oder DOS und eine vorhandene Apparatur zum herkömmlichen Destillieren (von Hand) benötigt. Durch die Tatsache, dass diese Ausrüstung im finanziellen Möglichkeitsbereich privater Haushalte liegt, wird es diesen ermöglicht, durch Destillation eigenen Essig oder Alkohol zu gewinnen. Ebenso besteht die Möglichkeit, Drogenextrakte herzustellen, oder als Hobbybiologe oder Hobbykriminalist tätig zu werden, und die Apparatur zur Durchführung von Analysen, zum Nachweis von Bodengiften oder zum Reinigen von Chemikalien zu verwenden.
Es war aber nicht nur Ziel, den Vorgang der Destillation von Hand zu erleichtern, sondern auch, ein praktisches Hilfsmittel für den Schulunterricht zu erstellen; denn durch die Themenvielfalt der Arbeit wird ein fächerübergreifendes Lernen anhand von praktischen Beispielen ermöglicht (s. Lehrmöglichkeiten).
Die Idee:
Die Idee zum Bau eines solchen Interfaces kam mir schon vor zwei Jahren. In der Schule hatten wir im Chemieunterricht destilliert und ich wollte das zu Hause auch machen. Ich stellte mich also für mehrere Stunden mit einem kleinen Spiritusbrenner in den Keller, und musste feststellen, wie nervend es sein kann, längere Zeit lang immer nur den Spiritusbrenner unter den Kolben und wieder weg zu schieben.
Also nahm ich mir vor, diesen Vorgang zu automatisieren.
Die erste Umsetzung:
Da alles schnell gehen musste - ich wollte schließlich möglichst schnell ein Resultat sehen - bastelte ich mir aus einer LEGO-Eisenbahn auf Schienen eine Transportplattform, auf dem der Spiritusbrenner sich hin und her bewegen konnte. Um in der Lage zu sein, die Position des Brenners festzustellen, befestigte ich an den beiden Haltepunkten der LEGO-Eisenbahn, den jeweiligen Endpunkten der Schienen, Reed-Kontakte und an der Bahn selbst zwei Magneten. So konnte das Programm immer feststellen, ob der Brenner sich gerade unter dem Destillationskolben befand. Der Antrieb der Eisenbahn erfolgte über Relais und Transistoren, die der Computer über zwei Optokoppler ansteuerte.
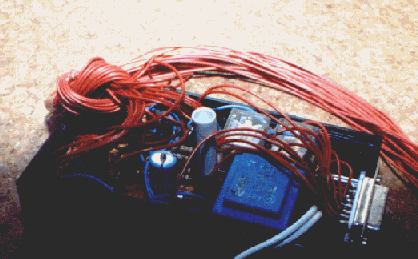
Da mir als Meßwerte nur analoge Ströme und Spannungen vorlagen, der Computer aber nur digitale Daten verarbeiten kann, entschied ich mich für den Kauf eines Analog-Digital-Wandlers. Dieser sollte die durch einen temperaturabhängigen Widerstand veränderte Spannung digitalisieren und über eine Schnittstelle an den Computer weiterleiten. Da mein Wissen über die Schnittstellen des Rechners aber nicht ausreichte, mußte ich mir eine Steuerkarte zulegen, mit der ich 24 Bit lesen oder setzen konnte.
Das nächste Problem bestand in dem Anschluß des Analog-Digital-Wandlers, eines 20-pol. ICs. Ich besorgte mir ein 14 Seiten langes Datenblatt, welches in Englisch verfasst war. Nach einiger Zeit hatte ich dann die wichtigen Stellen übersetzt und konnte mein erstes Interface aufbauen und in Betrieb nehmen. Es funktionierte auch alles korrekt; nur war die Apparatur etwas wackelig.
Die zweite Umsetzung:
Nach einiger Zeit begann ich mit der Konstruktion einer besseren mechanischen Lösung für den Transport des Spiritusbrenners. Ich baute eine neue Beförderungsplattform auf Schienen. Diesmal verwendete ich als Baumaterial kein LEGO, sondern Holz. Ebenso wie in der ersten Umsetzung bewegte sich der Brenner wieder auf einer Plattform auf Schienen hin und her. Da ich aber dieses Mal einen Schrittmotor für den Antrieb benutzte, entfielen die Reed-Kontakte, da das Programm die ausgeführten Schritte des Schrittmotors zählen und in eine Längenangabe umrechnen konnte. So war es möglich, die genaue Position des Brenners zu bestimmen. Ebenso war es nun möglich, die Geschwindigkeit der Transportplattform mit der Software zu steuern.
Diese Apparatur destillierte hervorragend! Sie hatte aber, wie ihr Vorgängermodell, keinen besonders guten Wirkungsgrad, da mehr Spiritus benötigt wurde als Alkohol produziert. Außerdem konnten auf Grund der Größe des Spiritusbrenners immer nur sehr geringe Mengen Alkohol oder Wasser destilliert werden.
Diese Apparatur kam nur noch wenige Male zum Einsatz, obwohl ich ursprünglich beabsichtigte, mit ihr am Wettbewerb teilzunehmen.
Die aktuelle Umsetzung:
Als meine Chemielehrerin von meiner Absicht erfuhr, bei dem Wettbewerb "Jugend Forscht" teilzunehmen, bot sie mir an, mir eine Apparatur der Schule zu leihen. Diese Apparatur enthielt neben einem Rundkolben, einem Stativ und einem Liebigkühler ein elektrisches Heizkissen und machte somit meine bisherigen Bemühungen, einen Spiritusbrenner zu bewegen, überflüssig. Erst jetzt kam ich auch auf die Idee, die Arbeit als Bausatz für den Unterricht an Schulen zu gestalten.
Mit diesem neuen Gedanken wurde auch mein altes Interface unbrauchbar. Es ist mehr ein allgemeiner Analog-Digital-Wandler, viel zu allgemein ausgelegt, um als einfacher Bausatz dienen zu können, und eignet sich aus diesem Grund nicht für einen solchen. Ich musste also die ganze Schaltung noch einmal neu entwerfen, einkaufen und aufbauen.
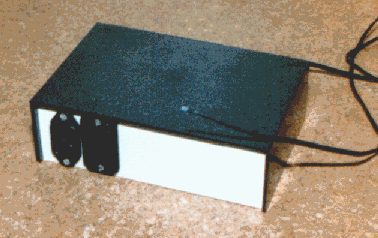
Ich begann also mit dem Bau eines neuen Interfaces, möglichst schlicht und einfach nachzubauen. Den Schaltplan und die Bauteile hatte ich Dank der Erfahrung mit dem bisherigen Interface schnell zusammen gestellt; nur die Platine brachte mich in zeitliche Schwierigkeiten.
Ich entschloss mich nämlich, die Platine für die Schaltung zu belichten und danach zu ätzen, d.h. das Platinenlayout erst vorzubereiten, dann auf die Platine zu übertragen und die freien Kupferstellen mit einem Ätzmittel zu entfernen. Ich entwickelte das Layout auf dem Computer und druckte es dann auf Umwegen auf eine Folie aus.
Da ich aber noch nie zuvor eine fotobeschichtete Platine belichtet hatte, verlief der erste Versuch auch direkt ergebnislos, und ich mußte erst einmal eine neue Platine besorgen. Erst im zweiten Anlauf erzielte ich dann gute Ergebnisse.
Die Bauteile waren dann nicht mehr schwer einzulöten. Die einzige Schwierigkeit stellte das Gehäuse dar, in das ich noch die verwendeten Stecker und Buchsen einsetzen musste. Bei dieser Arbeit war handwerkliches Geschick mit der Laubsäge gefragt. Auch die Software, mit der ich das Interface ansteuere, stellte kein Problem mehr da, und auch die anfangs vorhandenen Probleme mit der Schnittstelle des Computers waren beseitigt; nach längerem Forschen gelang es mir nämlich, das Interface über die parallele Schnittstelle des Rechners anzusteuern.
Die neue Apparatur arbeitete dann auch direkt beim ersten Versuch einwandfrei.
Die Apparatur:
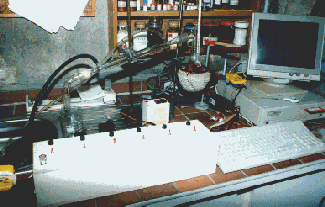
Mit dem Heizkissen wird der Inhalt des Rundkolben erhitzt. Der dabei teilweise gasförmig werdende Inhalt des Kolben kondensiert dann in dem Liebigkühler, der wiederum von der Pumpe mit Kühlwasser versorgt wird; es könnte auch ein direkter Wasseranschluß verwendet werden, um das Kühlwasser durch den Kolben zu pumpen, da ein solcher einen gewissen Wasserdruck aufweist. Da beim Vorstellen der Apparatur aber nicht unbedingt ein Wasseranschluß zur Verfügung stehen wird, kann der benötigte Druck durch eine Pumpe erzeugt werden.
Der Computer kann nun mit Hilfe des Interfaces die Veränderung des Widerstandes des Temperatursensors messen und so die Temperatur im Rundkolben ermitteln. Das Heizkissen wird dann bei Bedarf aus oder ein geschaltet und somit die Temperatur mit dem Heizkissen geregelt. Das Programm ist so in der Lage, eine vom Anwender eingegebene Temperatur beizubehalten.
Auf diese Art und Weise können verschiedene Gemische, deren Siedepunkte sich voneinander unterscheiden, voneinander getrennt werden.
Die Temperatursensoren:
Bei genauen Temperaturmessungen kommt es in besonderem Maße auf die Temperatursensoren an. Meine Schaltung ist auf solche mit linearem Verlauf und einem Wertebereich zwischen 1000W und 1400W ausgelegt, wobei der Wert des Widerstandes sich proportional zu dem der Temperatur verhält.
Mit dieser Differenz des Widerstandes muss nun eine möglichst große Spannungsdifferenz erzielt werden, um vom Analog-Digital-Wandler möglichst genaue und sinnvolle Werte zu erhalten.
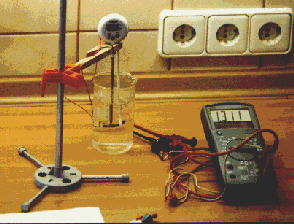
Bei diesem Problem half nun aber das Datenblatt des Analog-Digital-Wandlers weiter. Der Wandler bietet nämlich die Möglichkeit an, den zu messenden Bereich, der dann in 256 Einheiten zerlegt wird (1 Byte, welches nach der Wandlung ausgegeben wird), selber festzulegen. Aus diesem Grund ist es möglich, die unterste Spannungsgrenze und die Intervallgröße des zu messenden Spannungsbereichs festzulegen. Man muss lediglich entsprechende Spannungen an zwei dafür vorgesehenen Eingängen des Wandlers anlegen, wobei an dem Eingang, der die Intervallgröße festlegt, die Hälfte der eigentlichen Intervallgröße anliegen muss.
Auf Grund der unterschiedlichen Widerstandswerte der verschiedenen Temperatursensoren habe ich den Bereich etwas größer als benötigt gewählt. Mir ist es nämlich passiert, dass zwei Sensoren des gleichen Typs Abweichungen von bis zu 100W aufwiesen. Aus genau diesem Grund gab ich auch schließlich meine Bemühungen auf, eine Funktion für den jeweiligen Temperatursensor zu ermitteln, welche die in den Rechner eingehende Zahl des A/D-Wandlers in einen passenden Spannungswert umrechnet. Aus diesem lässt sich dann leicht mit Hilfe des Ohmschen Gesetztes der dazugehörige Widerstand und aus diesem mit Hilfe einer zweiten Formel die entsprechende Temperatur ermitteln. Der Aufwand, der betrieben werden musste, um die beiden Formeln zu erhalten, war sehr groß.
Zuerst musste eine Vergleichsmessung durchgeführt werden, bei der jeweils die Temperatur und der Widerstand des Sensors notiert werden mussten. Dazu mussten möglichst viele Messwertpaare genommen werden, um Fehlmessungen zu verdecken. Dann konnte dann ungefähre Formel für den Temperatursensor errechnet werden. War es jedoch nötig, einen Sensor auszuwechseln, mussten die gesamten Messungen mit dem neuen Sensor wiederholt werden. Aus diesem Grund ist es bei meiner aktuellen Arbeit nicht mehr nötig, diesen Messaufwand zu betreiben. Die neue Software fordert den Anwender bei dem Gebrauch eines neuen Sensors nur noch auf, den Temperatursensor auf zwei verschiedene Temperaturen zu bringen und diese anzugeben. Die Formeln erstellt sie dann von allein.
Ein mehr mechanisches Problem mit den Temperatursensoren ergab sich in ihrer Anwendung. Es ist nämlich nicht möglich sie mit ihren blanken Anschlüssen direkt in ein flüssiges Medium einzuführen, ohne erhebliche Fehlmessungen befürchten zu müssen. Als Lösungen kamen daraufhin nur zwei Möglichkeiten in Frage:
Zum Ersten konnte der Temperatursensor mit der flachen Seite von außen an dem Gefäß mit der zu erwärmenden Flüssigkeit befestigt werden. Diese Lösung erwies sich allerdings nicht als sehr effektiv, da der Sensor immer von der schlechten Wärmeleitfähigkeit des Gefäßes und von der auf der anderen Seite anliegenden Zimmerluft beeinflusst wurde.
Übrig blieb also nur die zweite Möglichkeit: Der Sensor mußte wasserdicht verpackt werden. Nach einigen Versuchen hatte ich dann eine effektive Lösung gefunden. Ich schloss den Sensor in einen Schrumpfschlauch ein, der in der Lage ist, den benötigten Temperaturen Stand zu halten. Bisher funktioniert diese Lösung auch einwandfrei.
Die Hardware:
Wie schon erwähnt, besteht die Hardware aus einem Interface, welches an die parallele Schnittstelle eines Computers anzuschließen ist. Des weiteren ist ein Anschluß für einen Stereo-Klinkenstecker vorhanden, an den der temperaturabhängige Widerstand angeschlossen wird, und zwei Anschlüsse in Form von Kaltgerätestecker und -buchse für die Stromversorgung. Dabei dient der Kaltgerätestecker als Eingang und die Kaltgerätebuchse als Ausgang. An sie kann das Heizkissen angeschlossen werden.
Im Inneren des Interfaces befinden sich drei einzelne Abschnitte:
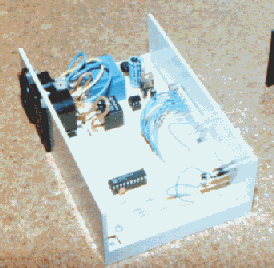
Der zweite Abschnitt besteht aus der Steuereinheit für den 220 V~ Ausgang. Diese Einheit besteht aus einem Optokoppler, einem npn-Transistor und einem Relais mit einem maximal zulässigen Schaltstrom von 2,5 A. Der Optokoppler (N28) ist dabei zum einen an den Stift 16 der parallelen Schnittstelle angeschlossen, zum anderen schaltet er einen Strom, den der Transistor dann verstärkt, um damit das Relais zu steuern.
Die dritte und komplizierteste Einheit stellt dann den Meßbereich dar. Diese Einheit besteht ihrerseits aus sechs Widerständen, zwei Kondensatoren, dem Temperatursensor und dem A/D-Wandler (ADC08041CN).
Fünf Widerstände und der Temperatursensor sind als Spannungsteiler geschaltet und produzieren die Spannungen für den Eingang der unterste Messgeräte, den der Messintervallgröße und die zu messende Spannung selbst. Der eine Kondensator (56 pF) produziert zusammen mit einem Widerstand (10 kΩ) die interne Taktfrequenz des A/D-Wandlers und der andere Kondensator (10 μF) glättet noch einmal die Versorgungsspannung des ICs. Die acht Ausgänge des 20-pol. Bausteins, an denen später die Meßdaten anliegen, sind direkt mit der parallelen Schnittstelle verbunden. Die Meßwerte werden nur angelegt und es werden keine Informationen an den Rechner gesendet, wie es ein Drucker oder Scanner machen würde, um den Rechner aufzufordern, die anliegenden Daten zu lesen. Dies ist nicht notwendig, da sie mehrmals in der Sekunde - abhängig vom internen Takt des Bausteins - erneuert werden.
Das Programm hat die Möglichkeit, über den Stift 14 den A/D-Wandler neu zu starten, bzw. einen Reset durchzuführen, indem es einen HIGH-LOW-HIGH Logikpegel über diesen Stift sendet. Dieser Vorgang sollte möglichst vor jeder neuen Messung erfolgen, um eventuelle Messfehler auszuschließen.
Die Software:
Die Software (interfac.exe) besteht aus einem einfach aufgebauten Programm, welches mit der Programmiersprache Turbo-Pascal für das Betriebssystem DOS geschrieben worden ist. Außerdem legt das Programm nach dem ersten Start eine Informationsdatei (setup.inf) an, in der es die Adresse der verwendeten Schnittstelle sowie die Ergebnisse der Kalibrierungsmessung ablegt.
Die Software ist so ausgelegt, dass sie bei jedem ersten Start den Anwender zu einer Kalibrierungsmessung auffordert. Dieser Vorgang kann auf Wunsch des Anwenders auch zu jeder beliebigen Zeit wiederholt werden.
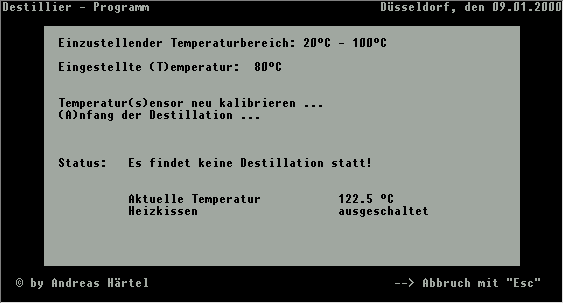
Zusätzlich muß bei jedem ersten Programmstart die Adresse (IRQ) der verwendeten parallelen Schnittstelle angegeben werden, an der das Interface bei späteren Sitzungen angeschlossen wird. Wird diese Adresse nicht korrekt angegeben, so kann das Programm nicht mit dem Interface kommunizieren; es könnte sogar einen Absturz des Computers herbeiführen. Vor dem ersten Start sollte diese Adresse also sorgfältig nachgeschaut werden.
Das Programm arbeitet mit einer ganz schlichten Oberfläche. Manche der Buchstaben auf dieser Oberfläche sind eingeklammert. Mit ihnen kann durch Eingabe auf der Tastatur die entsprechende Funktion ausgeführt werden.
Intern arbeitet die Software mit einer REPEAT-UNTIL Schleife, in der die Temperatur gemessen und der Tastaturpuffer auf Tastenbetätigungen kontrolliert wird. Je nach eingestellter Temperatur wird dann der Schaltausgang des Interfaces geöffnet oder geschlossen. Bei vorliegenden Daten im Tastaturpuffer werden diese ausgewertet.
Lehrmöglichkeiten:
Wie schon erwähnt, soll unter anderem die Wissensvermittlung anhand von praktischen Beispielen ein Ziel meiner Arbeit sein. Zu diesem Zweck habe ich auch ein Handbuch entworfen, welches unter anderem dieses Kriterium behandelt.
Lehrern und Schülern soll meine Arbeit - der Bausatz, die Software und das Handbuch - ein Hilfsmittel für einen Unterricht mit praktischen Hilfsmitteln sein.
Aufgrund der vielen Themen, die diese Arbeit beinhaltet, ist sie in vielen Fächern anzuwenden. Dadurch wird auch ein fächerübergreifender Gemeinschaftsunterricht möglich, in dem die Schüler in kleinen Gruppen zusammenarbeiten können, und dabei verschiedene Aufgaben erledigen, die sich nachher zu einem Ganzen vereinen lassen. So kann schon an der Schule auf später im Berufsleben vorkommende Teamarbeit vorbereitet werden, die wohl in den meisten Firmen praktiziert wird.
Der Bausatz bietet Unterrichtsmaterial für folgende Fächer: Physik, Informatik, Chemie und evtl. Kunst. Allgemein ist er in das Gebiet der Technik einzuordnen.
Das Handbuch:
Das Handbuch beinhaltet eine Anleitung zum Erbauen des Interfaces und des Temperatursensors, sowie einige Vorlagen und Beispiele. Außerdem gibt es Vorschläge und Informationen zu der Anwendung des Bausatzes im Unterricht und zu dem Aufbau des Interfaces.
Es soll dabei helfen, Wissen anhand von praktischen Beispielen zu vermitteln, durch die Arbeit selbst Wissen vermitteln und das eigene Interface aufzubauen und in Betrieb zu nehmen. Ebenso gibt es Hinweise und Beispiele zum erstellen einer eigenen Treibersoftware.
Außerdem wird durch den Einsatz von Zeichnungen, Fotos und Tabellen eine gute Übersichtlichkeit erzielt.
Ein Anwendungsbeispiel:
Eine Schule erwirbt den Bausatz mit dem dazugehörigen Handbuch oder nur das letztere, denn es ist auch möglich, die Einzelteile des Bausatzes selber zu erwerben; eine ausführliche Beschreibung liegt dem Handbuch bei!
Zuerst einmal kann nun die Wirkung von Säuren auf Metalle besprochen werden, indem als Beispiel die Platine mit aufgetragenem Layout geätzt wird. Als Layout kann wahlweise die beiliegende Vorlage verwendet werden, oder ein eigenes Layout anhand des Schaltplanes entworfen werden. Um das Layout von der Folie auf die Platine zu bringen, muss es entweder abgezeichnet werden oder eine fotobeschichtete Platine belichtet werden. Dabei kann das Entwickeln von Filmmaterialien geübt werden.
Ist die Platine dann fertig erstellt, so kann beim Einsetzen der Bauteile der Umgang mit dem Lötkolben gelernt werden. Um die fertige Schaltung dann in ein Gehäuse einzubauen, ist es nötig mit einer Laubsäge umgehen zu können, um passende Öffnungen für die Anschlußstecker zu schaffen. Ist das Interface dann fertig aufgebaut, ist es möglich das beiliegende Programm zu verwenden oder mit Hilfe des Handbuches ein eigenes zu programmieren.
Natürlich können während des gesamten Bauvorgangs die Berechnungen nachvollzogen werden, Kenntnisse über verschiedene Bauteile oder Programmierbefehle erworben werden oder Brückenschaltungen, physikalische Einheiten und Bits und Bytes besprochen werden.
Zu guter letzt ist es möglich, die Siedepunkte verschiedener Stoffe mit Hilfe des Interfaces zu untersuchen.
Die aufgetretenen Probleme:
Natürlich ist es mir nicht möglich, hier jedes kleine Problem ganz genau zu beschreiben, das bei der Arbeit an diesem Thema auftrat. Ich werde aber die wichtigsten und deren Lösung hier kurz beschreiben!
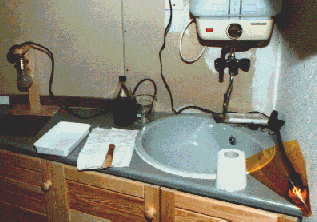
Platinenlayout: Ein weiteres Problem entstand, als ich das aktuelle Interface baute. Ich hatte ein Layout für die Platine auf dem Rechner vorbereitet und musste dieses nun auf die kupferbeschichtete Platine übertragen. Es ergaben sich zwei Möglichkeiten. Zum einen konnte ich das Layout einfach abzeichnen - abpausen ist leider nicht möglich - , zum anderen kann das Layout auch mittels der Fototechnik auf die Platine
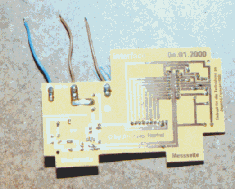
A/D-Wandler: Ein Problem ganz anderer Art stellte der Anschluß des A/D-Wandlers dar. Da das Datenblatt des Bausteins in Englisch verfasst war, interpretierte ich es lange Zeit falsch. So verbrachte ich dann Stunden mit der Suche nach nicht vorhandenen Fehlern, bis mir dann irgendwann die Idee kam, das Datenblatt erneut zu lesen. Da sich meine Englischkenntnisse seit der falschen Interpretation verbessert haben, verstand ich beim erneuten Lesen mehr und entdeckte meine Fehler und eine Möglichkeit, den Meßbereich des Bausteins zu optimieren.
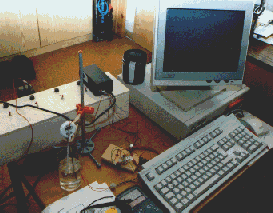
Wahl der Widerstände: Ein eher leicht zu lösendes Problem tat sich bei der Wahl der Widerstände auf. Ich verwendete lange Zeit lang solche mit 5% Toleranz, was natürlich eine gewisse Ungenauigkeit mit sich bringt. In dem aktuellen Interface habe ich solche mit 1% Toleranz verwendet. Außerdem musste ich mit den Widerständen verschiedene Spannungen erzeugen. Aus diesem Grund erstellte ich eine Excel-Tabelle, mit deren Hilfe man die richtigen Widerstandswerte leichter berechnen kann. Die Widerstände mussten aber vor allem auch zu dem Temperatursensor passen.
Anschluß an den Rechner: Weitere Probleme ergaben sich mit der von mir verwendeten Schnittstelle zum Rechner. Anfangs benutzte ich nämlich ein spezielles Interface, welches mir 24 frei programmierbare Ein- bzw. Ausgänge zur Verfügung stellte, da ich die Belegung der parallelen Schnittstelle des Computers nicht verstand. Um aber meine Arbeit möglichst preiswert und anwenderfreundlich zu gestalten, und auf das extra Interface zu verzichten, habe ich in mehrstündiger Arbeit die parallele Schnittstelle durchgemessen und die Ergebnisse notiert. Daraufhin war es mir möglich, das Interface über diese Schnittstelle zu betreiben.
Kühlung: Ein nicht so wichtiges Problem eher anderer Art ergab sich in der Verwendung einer Pumpe. Anfangs verwendete ich zur Kühlung des gesiedeten Stoffs, der destilliert werden sollte, eine alte Pumpe. Immer wenn ich diese ein oder aus schaltete, stürzte der Computer, der am selben Netz hing, ab. Lange Zeit suchte ich den Fehler in dem Steuerprogramm, bis ich entdeckte, dass die Pumpe keinen Kondensator besaß, um Spannungsspitzen abzufangen, die beim Ein- oder Ausschalten des Motors entstehen. Diese Spannungsspitzen brachten den Computer jeweils zum Absturz. Die nun verwendete Pumpe besitzt einen solchen Kondensator. Das Problem ist also für die momentan verwendete Apparatur nicht störend. Als Lösung kann aber ein genügend starker Kondensator über die Anschlüsse der Pumpe geschaltet werden.
Verbesserungsvorschläge für zukünftige Arbeiten am Projekt:
Eine Änderung der Hardware, wäre an dem Temperatursensor vorzunehmen. Dieser könnte nämlich am besten in einem dünnen Metallrohr mit Meßspitze untergebracht werden, in das er sich genau passend einfügen läßt. So wäre er robuster und gleichzeitig immer noch leistungsstark.
Natürlich kann auch das Handbuch jederzeit verbessert und erweitert werden.
Die eigentlichen Verbesserungen müssten an der Software vorgenommen werden. Diese müßte zum Beispiel die Adresse der Schnittstelle, an die das Interface angeschlossen ist, von alleine ermitteln können. Auch ließe sich im Bezug auf die grafische Oberfläche und die Bedienerfreundlichkeit noch einiges ändern. So könnten zum Beispiel ein Menü, eine Maussteuerung oder eine Zustandszeichnung eingefügt werden. Weiterhin wäre es sinnvoll, das Programm selber für Windows auszulegen, d.h. als Windows-Programm zu programmieren.
Quellenangaben:
- Datenblätter zu den verwendeten ICs von Conrad-Electronic GmbH
- DeskJet 500 Drucker Handbuch, 1990 Hewlett-Packard Company, Teilnummer C2106-90018
- Fotobeschichtetes Basismaterial Arbeitsanleitung, 1989 Bungard Elektronik
- 8255-I/O-Karte, Best.-Nr. 967700, 1988 Conrad-Electronic GmbH
- Experimentieranleitung KOSMOS HiTec electronic + PC, Franckh-Kosmos Verlags-GmbH & Co., Stuttgart 1994
- LexiROM Version 2.0, 1995-1996 Microsoft Corporation und Bibliographisches Institut & F. A. Brockhaus AG
- CD-Römpp Chemie Lexikon, Jürgen Falbe und Manfred Regitz, Georg Thieme Verlag, Stuttgart 1995
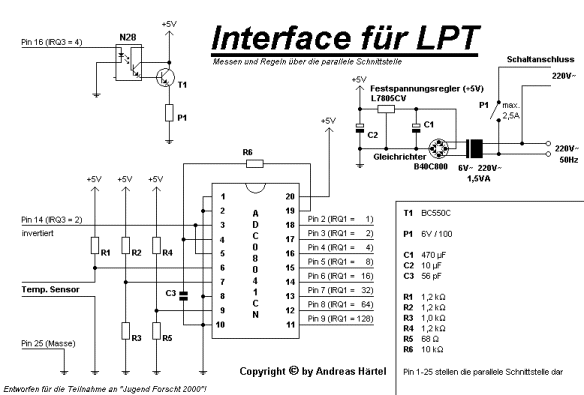
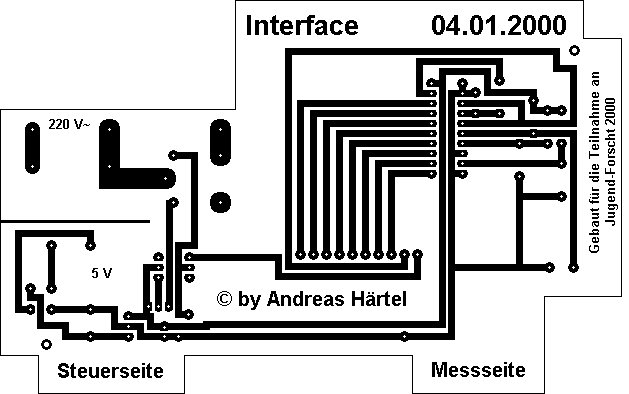
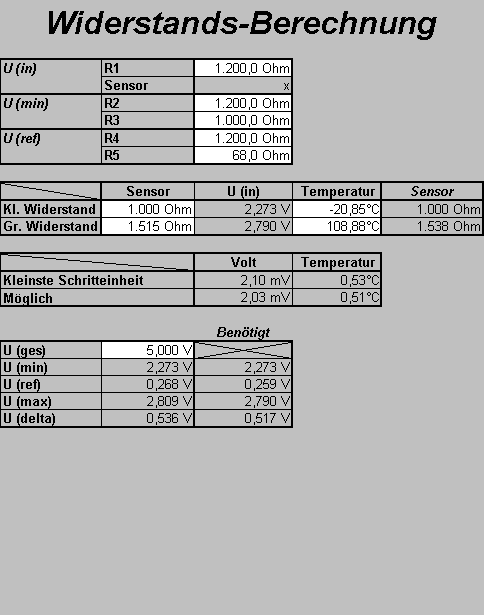
© A. Härtel (2017)